Driving Efficiency through remote monitoring
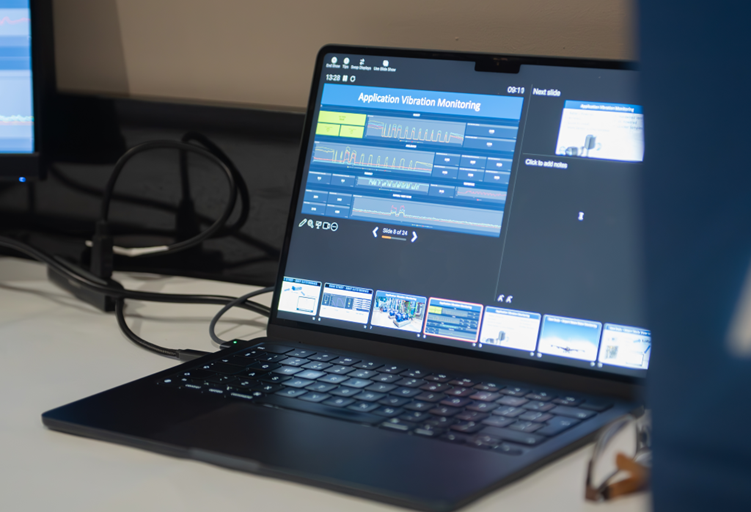
Driving Efficiency through remote monitoring
Background
When we rely on information to make critical decisions, data capture needs to be done in a methodical and meaningful way. Especially when we need to call on that data later to help us in some way. Whether data is collected manually or electronically, getting reliable answers to the questions that we have is important.
Our customer started with a manual approach. Their factories housed large tanks that contain bread making ingredients such as yeast and flour. Every day, those levels would need to be monitored and reported so they could make an educated judgement on when was the best time to re-order the raw ingredients. This approach yielded accurate results but with a high labour commitment, along with the associated costs of taking time out of the day to record the levels. Because the customer had multiple sites with multiple tanks, these costs were significant. Therefore, it made sense to implement a more efficient way to carry our this regular and very critical task.
The Solution
We worked together with our customer to implement a solution that would yield just as accurate results as before, but that would go on to save an immense amount of time, energy and reduce costs and potential downtime.
After discussing options, we settled on the idea of implementing a semi-automatic approach to the re-ordering of their raw materials. We devised a cloud dashboard with a modified user interface, showing our customer exactly the information they wanted to see, when they wanted to see it. We also set the correct administrative levels as discussed, giving users just as much control as they needed.
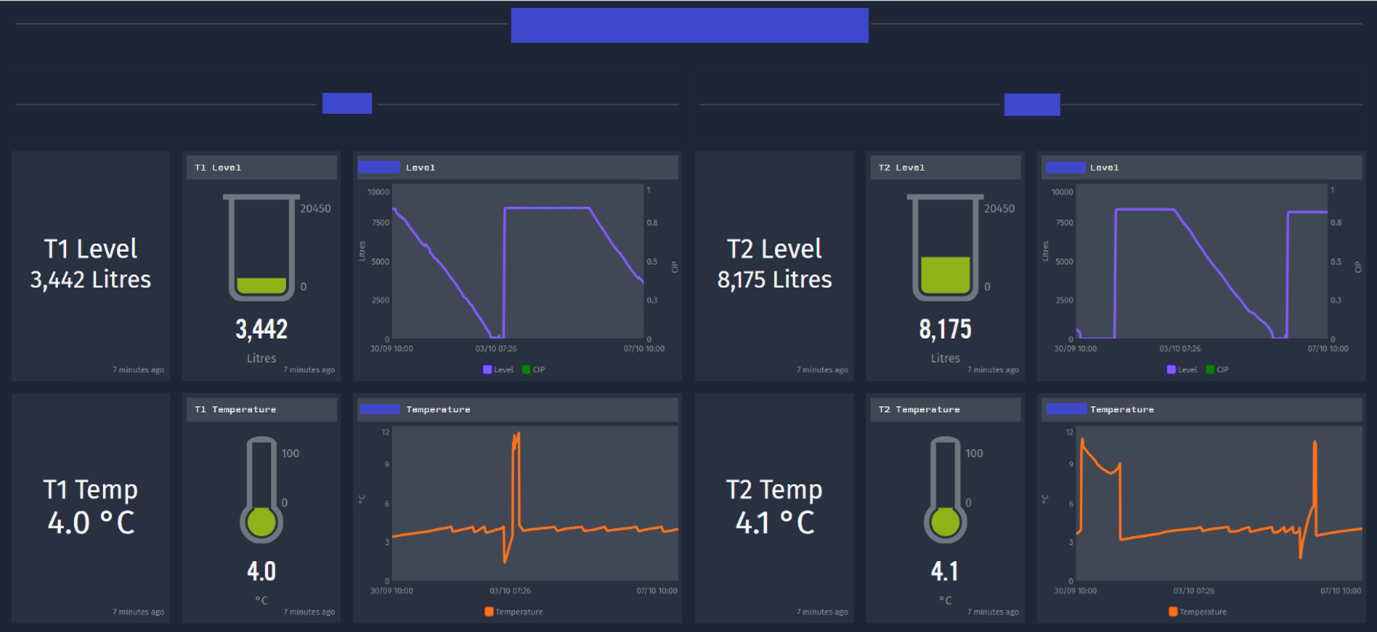
From the dashboard, we could visualise the tank levels in real-time, set up automatic alerting and provide a reliable way of reading the results to make the re-ordering process more efficient.
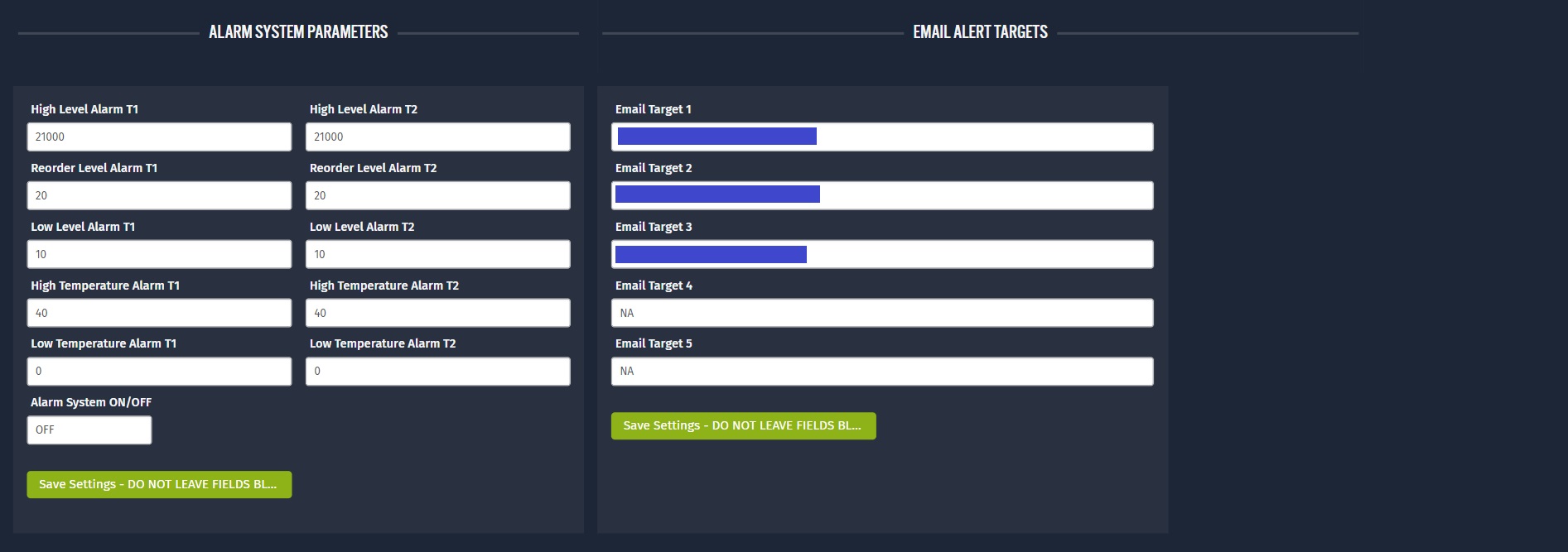
The Technical bit
To monitor the levels – tank volume and temperature, we first needed to tap into the established level and temperature monitoring hardware. We deployed an Advantech ADAM-6017 8-ch Isolated Analog Input Modbus TCP Module to capture the raw, analogue inputs to the device which translated the captured data to MQTT and securely passed this information to the cloud. As the project progressed and the customer could see the benefits of the newly introduced system, we gained further process efficiency by installing an ADAM 6050 unit, which when configured would allow us to work with the factory alerts regarding the plant CIP (Cleaning In Progress) activities. This helped to save on logistical conflicts of raw materials being delivered while the plant was not in a state to receive a bulk delivery. It also meant that head office was aware that the tank was being used for plant cleaning and not reading false data because of the CIP processes.
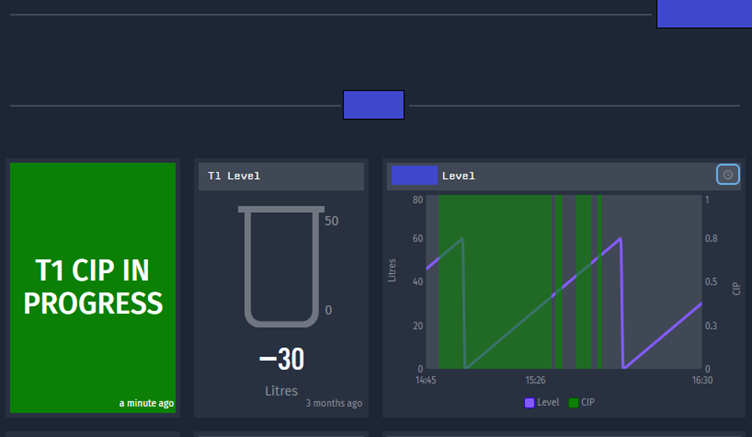
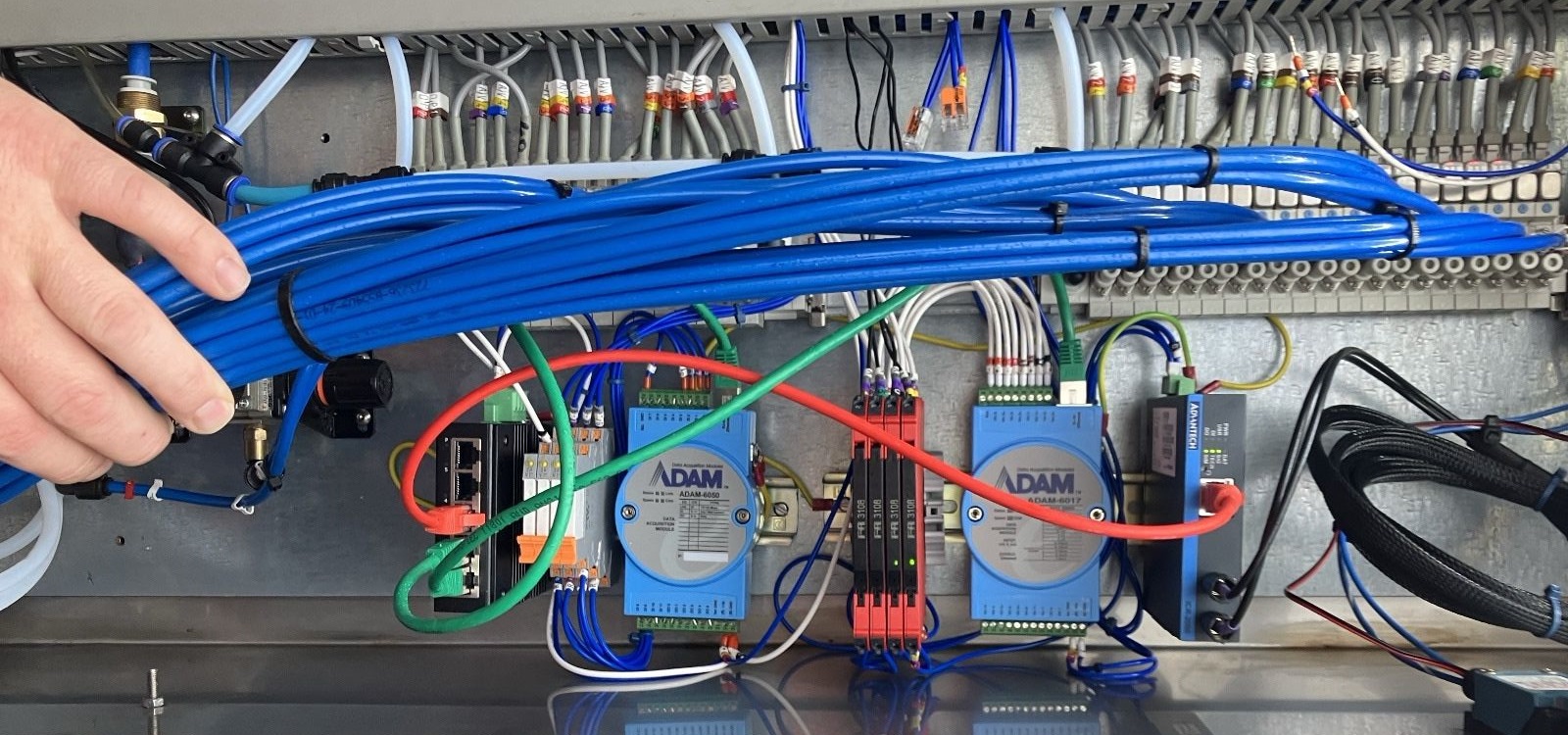
In order to give the ADAM units secure connectivity to the cloud (independent from the factory networks), we used an Advantech ICR-2431 Industrial Router with one port dedicated to the analogue module and the other to the digital module. Due to the rigorous cleaning exercises that were carried out regularly on the site, the router was to be housed in an enclosed, waterproof cabinet. This meant that we would have to use an antenna that could be externally mounted on the cabinet and withstand regular jet washing in an industrial environment. We opted for the IP68 rated PUCK-2 antenna from Poynting Antennas. The ruggedised design of the PUCK-2 along with its extensive range of mounting options made this install simple and very effective.
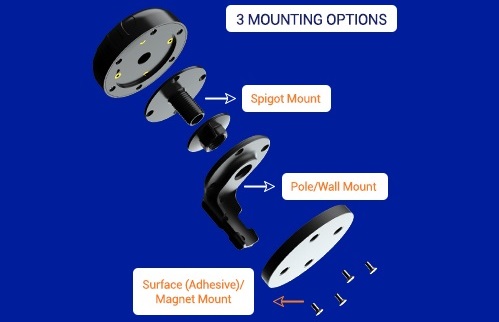
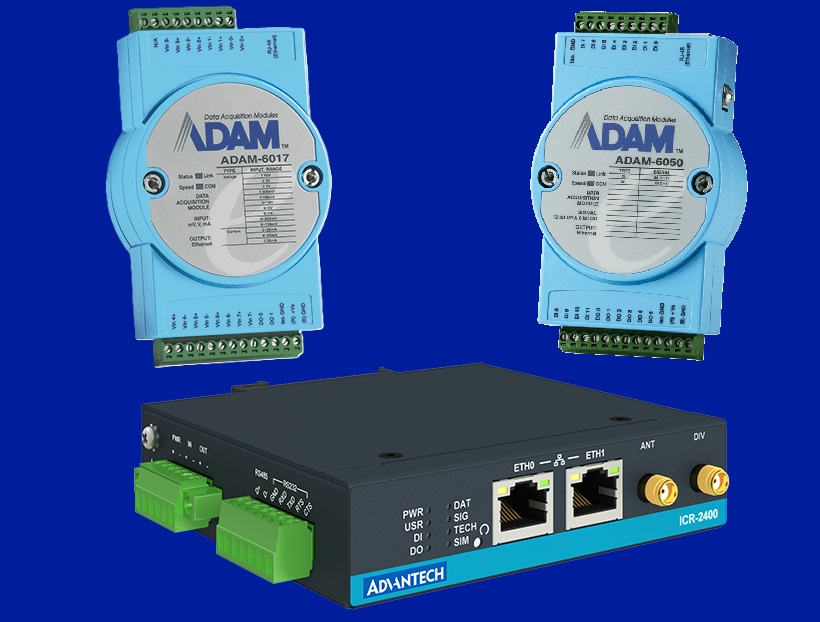
The Results
· Our customer was able to save time and costs associated with physically taking readings.
· Readings were reliable, visible and with user permissions set by admins, allowing information to be shown to those who needed it.
· They were able to visualise levels, temperatures and alarms on a customer configured dashboard, showing them exactly what they wanted to see. Dashboard pages were displayed by site with graphs, charts, units and more customised by the customer.
· Logistical bottlenecks were reduced by implementing a system which showed in real time when CIP processes were taking place, reducing wait times for tankers or “turn-aways” at the gate. This alone saw cost savings due to re-booking tanker deliveries and penalties for non-delivery.
· System implemented with an “Air-Gap” between the new installation and any existing network on site, allowing totally independent access via a secure router to the internet.